
Friday, September 19, 2014
Fuse Box Toyota 2000 Corolla CE Instrument Panel Diagram
Fuse Box Toyota 2000 Corolla CE Instrument Panel Diagram
Fuse Panel Layout Diagram Parts: wiper fuse, stoplamp fuse, taillight fuse, noise filter, I/UP fuse, ECU-IG fuse, ignition fuse, turn fuse, gauge fuse, power steering fuse, door fuse, cigar lighter, defogger, power window.
Fuse Box Toyota 1995 Supra Engine Compartment Diagram
Fuse Box Toyota 1995 Supra Engine Compartment Diagram
Fuse Panel Layout Diagram Parts: A/C magnetic clutch relay, fog light relay, headlight relay, heater relay, fan relay, ABS system, starter relay, daytime running light, horn relay, dimmer relay.
Fuse BOx BMW Z3 Underdash 1996 Diagram
Fuse BOx BMW Z3 Underdash 1996 Diagram


Fuse Panel Layout Diagram Parts: ABS system, motorsport, airbag, air conditioning, automatic transmission, anti theft sytem, cigar lighter, clock, connector for optional, cruise control, cruise seats adjustment, electronic immobilizer, exhausy gas diagnosis, fuel pump, headlight cleaning system, heated seat window, heated blower, brake light, parking light, reversing light, side ligth, low beam headlight, interior light, high beam headlight.
Fuse Box Toyota 93 Camry 2200 Diagram
Fuse Box Toyota 93 Camry 2200 Diagram
Fuse Panel Layout Diagram Parts: ABS ECU, door lock control relay, cooling gan ECU, center air bag sensor, fuse/relay block, integration relay, A/C amplifier, shift lock control ECU, daytime running light relay,fuse relay, engine control module, electronic control transmission ECU, junction block, cruise control ECU.
2 x 30W dual bridge car radio amplifier
![]() |
2 x 30W dual bridge car radio amplifier TDA7394 |
Fuse Box Toyota 2008 Prius Diagram
Fuse Box Toyota 2008 Prius Diagram
Fuse Panel Layout Diagram Parts: Power outlet, Power windows, Multi information display, Electric power steering, Gaug and meter, Power windows, Rear Window defogger, Multi-information display, Air conditioning system, Hybrid system, Tail lights, License plat light, Parking light, Multi information display, Clock, Back up light, Emergency flasher, Power windows, On-board diagnosis system, Stop light, Power door clock system, Outside rear view mirror heater, Windshield wiper, Rear wiper, Washer, Smart entry and start system.
Thursday, September 18, 2014
TDA2822M Simple low power stereo amplifier
I have also seen this chip in use in PC speakers, a pair I got free when I brought a computer case claimed 120W PMPO. Well I wont lie like they do, this amp is only capable of 700mW per channel from a 6V power supply into 8 ohms (should be over a watt with 12V). This amp can also function well as an amp for headphones, providing 20mW into 32 ohms from 3V. I would have used it for that purpose in my main system, but unfortunately, space was limited and all I could do was run some resistors in series with the output to cut down the volume for headphones. So what have I done with these amps then? Well recently I have rebuilt a pair of speakers I had to be amplified with this amp. The speakers are quite large 4in speakers, but the TDA2822M will provide over a watt into each from the 12V PSU I am using. With built in transformer, these speakers easily impress more then most cheap walkman and PC speakers. Update: I have changed my small stereo speakers from a two TDA7052 amps to one TDA2822M amp.
This is because my TDA7052 circuit eventually failed. I guess this is so because the outputs from the TDA7052 are bridged and the removal and insertion of the 3.5mm plug that I used to connect the other speaker to the one with the amplifier circuit in would short the circuit momentary. The new circuit will make use of the TDA2822Ms non-bridged output which is still capable of nearly as much power (enough for the reason I built the speakers). The other amp I built was brought as a project kit and uses a similar circuit, the advantage of course was I didnt need to build the board. I used this amp in a small (ish) FM radio.
Dont ask how I made a stereo FM radio circuit because the circuit was just re-used from a rather sorry. It does have LW and MW too, but these dont work properly. The speakers are just simple elliptical speakers, but quality is bad at all, although it needs a regulated PSU because that digital clock I put in makes the amp hum if it runs off the same unregulated PSU.
Construction
This amp can also be very portable, as before I built the radio, I used the amp in a small pair of Walkman type speakers (that were passive). Only from 3V, there was a lot more volume then having them just passive, I recall people were quite impressed (although as you can guess the tone from the speakers was poor). Extra (simple) parts you may want to add to the schematic could be: 3.5mm jack input socket A power switch Batteries 2.1mm power plug (for external PSUs) - if wired correctly, this should disconnect the batteries when a plug is pushed into the socket. Bridge Version There is a bridge variant of this chip available in the datasheet should it be required. It is smaller still then the stereo version of the chip and should provide output levels similar to or even greater then, the TDA7052.
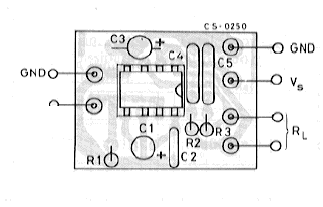
Again, this circuit is simply taken from the datasheet and you may need to modify it to include a single gang volume control. Please refer to the datasheet for schematics, components their values. Thats about all that can be said about this amp because so many applications are possible from it - it is very cheap too, however if you want that extra power, using two TDA7052 amps is also simple and will give you a little more power. Remember that the TDA7052 amplifiers are bridged and may not be suitable for some situations.
Copyright Site design, content and images © Daniel Clarke 2004 Construction made using JHTMLEd - copyright © Daniel Clarke 2004
Article from::: www.electro-dan.co.uk Read More at : http://www.electro-dan.co.uk/electronics/TDA2822.html
Building with Acrylic
Acrylic sheeting is widely known as Plexiglas©. Plexiglass©, however, is the name given to acrylic sheeting manufactured by Atofina. The same acrylic type sheeting is also known by the names Acrylite©, Lucite© and Perspex©. From this point on, Ill refer to it simply as acrylic.
Before we go any farther... Do not peel the protective coating from the sheet until the last possible moment. Acrylic sheeting is very easy to scratch. It may be even easier to scratch than CDs.
Cutting Acrylic:
There are a couple of different ways to cut acrylic. Since my experience is mainly with thin acrylic sheeting (1/2" or less), thats what Ill cover.
Table/Circular Saw:
For rough cutting acrylic, you can use a table saw or a circular saw with a fine blade. Blades with fine closely spaced teeth (like those used for plywood) will work relatively well. Blades with widely spaced teeth (like the type used for cutting MDF) will cause a lot more chipping. Ive used an Oldham B7254760 on a circular saw with good results. When using a hand held circular saw, use a guide to make sure you get a straight cut with minimal chipping. There are blades made specifically for cutting acrylic. If youre going to be cutting a lot of acrylic or are using very expensive (thick) material, you need to invest in a blade specifically designed for cutting plastics and laminates.
Jig Saw or Band Saw:
Jig saws can be used to cut acrylic when you need something other than a straight cut. To reduce the work of cleaning up the cut, use the finest blade that you can find. Blades with reduced depth (like those used for scroll work - shown below) will work best due to less friction and less resistance when turning the blade. Youll have to experiment with cutting speed to see what works best. Too much pressure can cause excessive chipping. Going too slow may cause the acrylic to melt. If the acrylic melts when cutting, use a light lubricating oil. Have someone apply the oil to the blade as youre making the cut. DONT use an aerosol dispensed oil. The propellant may be flammable and may be ignited by the jig saw motor. Ive had good results with the blade shown below.
Router:
A router can be used to cut acrylic for either straight or curved cuts. For curved cuts, youll want to use a router with a collar and a guide (pattern or jig made with 1/4 inch plywood). Youll want to rough cut the material within ~1/8 of an inch of the desired finished shape. Trying to cut too much acrylic will lead to melting of the material. Again, youll have to experiment with the speed of the cut. To prevent chipping, make sure the blade is not allowed to break contact with the cut edge. If it does break contact with the material and you push the router blade back into the edge too quickly, the cutter may chip the acrylic. You also must make sure you have a sharp bit (carbide recommended) to prevent melting of the material. Again, youll have to experiment to see what works best for you.
Score and Break:
Thin acrylic sheets (less than ~1/4") can be cut much like regular glass. Instead of using a hardened wheel to chip a line in the glass, youll use a scoring tool to cut a deep scratch in it. The cutting edge of the scoring tool looks something like a single tooth of a table saw blade (but much thinner). You apply pressure to the tool and drag it along a straight edge guide (which should be clamped securely in place to prevent it from moving). You need to continue scoring the acrylic until the cut is ~1/8 of the way through the material (it may take 20 passes on 1/4" thick stock). After thats done, youll have to clamp it down on the edge of a table (or something similar). The edge of the table needs to align with the cut. The edge of the table needs to be perfectly square (a radiused edge on the table wont provide the proper stress along the desired cut line). It needs to be clamped very securely so that it can not flex or move. Youll then apply pressure to the piece thats beyond the edge of the table until it snaps. If it was cut deeply enough, it will break cleanly along the desired line. If it was not cut deeply enough, the cut (on the side opposite the scoring) can be as far outside of the desired cut line as the thickness of the material. The image below shows an inexpensive scoring tool (I think it cost ~$3)
Polishing the Edge of the Cut:
Depending on the quality of the cut and the desired end use, the edge may need to be polished. When using the acrylic as a window on a speaker enclosure or for an amp rack, youll probably want to polish the edge. To make things easy, use a rubber or foam block and waterproof sandpaper. Since it will be nearly impossible to keep the edge perfectly square, Ill usually round it off. With a foam sanding block, start with rough paper (~180 grit). Wet sand with lots of water until the edge is uniform and relatively smooth. Then change to finer and finer paper until you get a satin finish with 600 grit paper (180, 360 and 600 grit will work fine). Remember to use lots of water.
Flame Polishing:
After the edge is polished to a satin finish, you may want to get it to a glass like finish. To do this, you can use a propane torch. Let me recommend that you practice on a scrap piece first. Using a propane torch, you very quickly pass the torch over the edge. You must move the torch very quickly. If you go too slowly, the acrylic will melt and boil. This will leave bubbles in the surface. This is from heating the acrylic too deeply. You only want to heat the very outermost edge/surface to its melting point. This will allow it to flow into a smooth glossy surface. As long as youre moving very quickly along the acrylic, youre not likely to cause bubbles (even if youre using the hottest part of the flame).
Practicing Flame Polishing:
The material that a CD is made of reacts similarly to that of the acrylic sheeting. If you want to scuff up a CD with some 600 grit paper (and water), youll be able to remove most of the finer scratches and haze with the torch. Remember... Move VERY quickly along the surface. Allow the CD to cool between passes with the torch (just as you would when polishing acrylic). Dont you use a good CD. Try it with one that will not play. Heating the CD will cause it to cup slightly and it probably wont play anymore. This exercise is only to allow you too see how the process works. Two final suggestions... Dont burn yourself and dont burn your parents house down.
Drilling Acrylic
Spiral Bit:
Standard spiral drill bits will not work well on acrylic. Their cutting angle is too aggressive which causes it to try to cut too quickly. This will lead to cracking and chipping around the hole. If you want to use a bit that can be used for metal also, try a bit like the one shown in the following photo. You can see that the main cutting edge is flat instead of angled like a normal bit. This causes the material to be cut in a more controlled fashion. If you dont want to spend the money on a new bit, you can grind a regular bit to the same profile.
Forstner Bit:
Forstner bits are very high quality bits that are generally used for woodworking. They make a very clean hole with little or no chipping. When used for drilling acrylic, you may need to use a cutting lubricant. I generally use a 3 in 1 type oil. Apply the oil to the cutting surface prior to drilling and to the drill bit shaft as youre moving through the material. If the bit is used dry, the friction between the sides of the bit and the material will cause the acrylic to melt (very bad). When used with lubricant, the hole will be very clean.
Standard Woodboring Bit:
Some people recommend against using woodboring bits but Ive never had a problem with them. One advantage of the wood bit is the long centering point. This point will exit the other side of the material before the cutting edge. This allows you to turn the material over and drill from the other side. Since the cutting edge will not be pushing out as the bit cuts through surface of the material, there will be little or no chipping on either side of the material.
When using any of the different bits for drilling acrylic, you should:
- Go slow. Do not force the bit to cut too quickly.
- Use a drill press. This allows you to have much more control over the cutting speed and assures that youre drilling the hole perfectly perpendicular to the material. You should clamp small pieces down. If the bit grabs the material and spins it, it will cut you. Small pieces dont allow you to get a good enough grip to prevent the piece from spinning with the bit.
- Practice on a piece of scrap material. If you crack a piece of acrylic after youve already polished the edges, you are not going to be happy.
- If the acrylic melts as you drill through it (regardless of rate of rotation/feed), try using a light lubricating oil to reduce friction between the bit and the acrylic.
Fasteners:
When screwing a piece of acrylic down, youll need to use some type of washer under the screw. Fiber, plastic and rubber washers will work. If you cant find those types of washers, standard metal flat washers will be better than nothing. If you use washers, youre less likely to crack the material if the screw doesnt go in prefectly straight. Predrilling the hole in the wood will help assure that the screw goes in straight. When tightening the screws, do not overtighten (especially when the surface under the acrylic is not hard). If theres a soft gasket under the acrylic, overtightening the screw will cause the material to crack. You should also use pan head screws (those with a flat mating surface under its head). Using bevel or bugle headed (drywall) screws will cause the acrylic to crack
Build a Digital Theremin Wiring diagram Schematic
Digital Theremin Circuit Diagram

Solar Tracking System Wiring diagram Schematic
Fig. 1: Circuit of solar tracking system |
Fig. 1 shows the schema of the solar tracking system. The solar tracker comprises comparator IC LM339, H-bridge motor driver IC L293D (IC2) and a few discrete components. Light-dependent resistors LDR1 through LDR4 are used as sensors to detect the panel’s position relative to the sun. These provide the signal to motor driver IC2 to move the solar panel in the sun’s direction. LDR1 and LDR2 are fixed at the edges of the solar panel along the X axis, and connected to comparators A1 and A2, respectively. Presets VR1 and VR2 are set to get low comparator output at pins 2 and 1 of comparators A1 and A2, respectively, so as to stop motor M1 when the sun’s rays are perpendicular to the solar panel.
When LDR2 receives more light than LDR1, it offers lower resistance than LDR1, providing a high input to comparators A1 and A2 at pins 4 and 7, respectively. As a result, output pin 1 of comparator A2 goes high to rotate motor M1 in one direction (say, anti-clockwise) and turn the solar panel.
When LDR1 receives more light than LDR2, it offers lower resistance than LDR2, giving a low input to comparators A1 and A2 at pins 4 and 7, respectively. As the voltage at pin 5 of comparator A1 is now higher than the voltage at its pin 4, its output pin 2 goes high. As a result, motor M1 rotates in the opposite direction (say, clock-wise) and the solar panel turns.
![]() Fig. 2 Proposed assembly for the solar tracking system |
Similarly, LDR3 and LDR4 track the sun along Y axis. Fig. 2 shows the proposed assembly for the solar tracking system.
Nicad Battery charger include voltage limiting
See this below :
![]() |
Click to view Enlarge |
TA8210AH Audio Amplifier 2x22W
.jpg)
TA8210AH general description:
TA8210AH features:
- Peak supply voltage (0.2s): 50 V
- supply voltage VCC (DC): 25 V
- Operating supply voltage VCC (opr): 18 V
- Output current (peak): 9 A
- Power dissipation PD: 50 W
- Operating temperature: 30~85 °C
- Storage temperature: 55~150 °C
TA8210AH circuit diagram:

TA8210AH layout:


Wednesday, September 17, 2014
Arduino Based Capacitive Touch Screen
Building a touch sensing capability can help in providing communication between the microcontroller and the tablet. Capacitive touch Lcds function by sensing the capacitance changes on the Lcd. In this case, a large conductive brass plate is used to simulate touch. The surface area of the conductor used here to simulate the touch sould be large.
Testing can be done by touching the scrren with a wire and holding the other end. This may not work. This is made to work by sticking a piece of aluminum foil on to the Lcd and connecting the free end to the pin that is available on the arduino. The video shows the working of the capacitive touch Lcd. The setup is quite fragile and a little more schemary could improve its reliability. Thus the capacitive touch Lcd is done.
Fuse Box Ford 2003 Crown Victoria Diagram
Fuse Box Ford 2003 Crown Victoria Diagram
Fuse Panel Layout Diagram Parts: subwoofer amplifier, trailer exterior lamp relay, horn relay, lighting control module, air suspension compressor relay, air spring solenoid, Starter relay, head lamp, starter relay, generator, radio amplifier, police power relay, daytime running lamp, PCM power relay, cooling fan relay, rear window defrost relay, trailer turn, battery charging relay, police option fuse holder, electric fuel pump relay, anti lock brake module, electric brake controller, power door lock, power seat, trunk lid release, fuel filler door releas.